5 TON Water ChillER
5-ton Emerson Copeland air-cooled condensing unit, specifically designed for commercial and industrial cooling applications. This compact and efficient system features dual axial fans that ensure effective heat dissipation, along with a high-performance Copeland compressor, known for its durability and energy efficiency. The unit operates on a 3-phase 380–415V, 50 Hz power supply and uses eco-friendly refrigerants such as R-22, R-407C, or R-410A, depending on the configuration. It is mounted on a sturdy metal frame, which also houses a centrifugal water pump connected through insulated piping—indicating that this unit is likely used in a water chiller system or cold room application. The system is capable of handling a 5 TR (tons of refrigeration) load, making it ideal for medium-scale cooling requirements. It includes a digital control panel for temperature and pressure monitoring, along with standard safety features like overload protection and phase failure detection. This 5-ton unit delivers reliable performance with easy maintenance, making it a practical choice for commercial HVAC, cold storage, or process cooling setups.
3 Ton Air-Cooled Chiller Unit designed for small to medium-scale industrial or commercial cooling applications. The unit features a high-speed axial fan mounted in a blue powder-coated steel body, ensuring efficient air flow and heat dissipation. On the right side is an integrated electronic control panel, labeled with essential safety and operational indicators. The panel includes power indicators, emergency stop, automatic temperature control, and a digital display for temperature monitoring and settings. This chiller operates on a 3-phase, 415V power supply, suitable for industrial-grade power input. The unit is compact and robust, ideal for continuous operation in environments like plastic molding units, chemical processing, cold rooms, or laser cutting machines. It utilizes eco-friendly refrigerants and is designed with built-in overload protection, phase failure safety, and temperature regulation, ensuring smooth and safe operation. Its compact design makes it easy to install and maintain, while the external wiring and reinforced legs provide additional support and durability in demanding industrial settings.
3 TON Water ChillER
Sand Water Filter
The Sand Water Filter is used for filtering out all visible dust particles from water. To a certain extent, It also removes chemicals and odour from water.
The filter is made of Fibre Reinforced Plastic (FRP) and is therefore aintenance free. The FRP material is ideally suited for water filtration tanks and is very strong and rigid. The tank requires no painting and does not rust.
Water passes through three layers of special Quartz stones and sand and a layer of Activated Carbon. A 10 micron filter cartridge is also provided at its outlet to removetiny dust particles.
A system of pipes and ball valves is provided which are attached to the main portion of the tank. The filter can be connected to an overhead tank and the water flows through the filter by gravity. About 500 litters of water can be filtered per hour.
Other than periodic backwash and a change of carbon, the filter requires very little maintenance.
It is an ideal unit for Soda /soft drink makers, juice processing factories, Hostels, Hotels etc and wherever bulk drinking water is required.
Ultra Violet Water Filter
Ultra Violet Water Filter System is ideal for filtration of Bore well and Well water. It is a 3-in-1 filter system.
It has a 10 micron filter cartridge which removes all visible dust particles. The water then flows through an activated Carbon Cartridge which removes chemicals and odour. Then the water flows through the UV chamber where two UV lamps are provided. They help to eliminate bacteria, germs, pathogens etc.
The filter can process about 500 litres of water per hour. It can be connected to an overhead tank and the water will flow through it by gravity. There is no need for pumps.
It is wall mountable and easy to assemble. It requires very little maintenance and is user serviceable.
It is an ideal unit for Soda / Soft drink makers, juice processing factories, hostels, hotels, etc. and wherever
bulk drinking water is required.
Medium Size Carbonator – Regular Quality
This Medium Size Carbonator is a reliable and efficient solution designed for carbonating beverages like soda, water, and other soft drinks. Crafted with precision, it delivers consistent carbonation results, ensuring excellent taste and fizz retention in every batch. The unit is built using regular quality yet durable materials, offering a balance between affordability and functionality for medium-scale beverage production operations.Mounted securely on a robust MS (Mild Steel) stand, the carbonator is equipped with an automatic control system that streamlines the carbonation process by managing pressure, CO₂ flow, and liquid levels efficiently. This automated operation enhances productivity, reduces manual effort, and ensures safety during use. Ideal for businesses seeking a dependable carbonation unit without compromising on performance or quality.Medium Size Carbonator – Regular Quality
This Medium Size Carbonator is a reliable and efficient solution designed for carbonating beverages like soda, water, and other soft drinks. Crafted with precision, it delivers consistent carbonation results, ensuring excellent taste and fizz retention in every batch. The unit is built using regular quality yet durable materials, offering a balance between affordability and functionality for medium-scale beverage production operations.Mounted securely on a robust MS (Mild Steel) stand, the carbonator is equipped with an automatic control system that streamlines the carbonation process by managing pressure, CO₂ flow, and liquid levels efficiently. This automated operation enhances productivity, reduces manual effort, and ensures safety during use. Ideal for businesses seeking a dependable carbonation unit without compromising on performance or quality.Medium Size Carbonator – Regular Quality
This Medium Size Carbonator is a reliable and efficient solution designed for carbonating beverages like soda, water, and other soft drinks. Crafted with precision, it delivers consistent carbonation results, ensuring excellent taste and fizz retention in every batch. The unit is built using regular quality yet durable materials, offering a balance between affordability and functionality for medium-scale beverage production operations.Mounted securely on a robust MS (Mild Steel) stand, the carbonator is equipped with an automatic control system that streamlines the carbonation process by managing pressure, CO₂ flow, and liquid levels efficiently. This automated operation enhances productivity, reduces manual effort, and ensures safety during use. Ideal for businesses seeking a dependable carbonation unit without compromising on performance or quality.
Reverse Osmosis Filter Unit
Reverse Osmosis is a technology that is used to remove a large majority of contaminants from water by pushing the water under pressure through a semipermeable membrane. The unit consists of a comprehensive set of filters like –
Prefilter to remove dust
Carbon filter to remove chemicals and other off smells
Ultra violet lamps to kill harmful bacteria and viruses
Reverse Osmosis filter unit to remove contaminants
Ozonator (Optional)
Other filters can be added depending on the inlet water quality.
The whole unit is mounted on a skid so it is easy to transport and can be quickly installed. Each filter unit is connected to the next in line with necessary pipes and fittings. Pumps are also provided.
The different filter stages are selected depending on the quantity of water available and so a Water Test Report is essential. Based on the report, the system can be tailored to get best results.
The unit is easy to install and requires minimum maintenance. It is made for reliable performance.
Big Size Carbonator – Regular Quality
This Big Size Carbonator is a robust and efficient carbonation system designed to meet the needs of high-volume beverage production. Crafted with a large-capacity stainless steel tank, it is ideal for carbonating water, soda, and other soft drinks on an industrial scale. Despite its regular quality build, it ensures stable performance, consistent carbonation, and long-term reliability.
The carbonator is mounted on a strong Mild Steel (MS) stand for added durability and support. It features an automatic control system that regulates pressure, CO₂ flow, and fluid dynamics with precision, making the process seamless and user-friendly. Perfect for businesses looking for an affordable yet high-capacity carbonation solution, this unit delivers both performance and productivity without compromise.
Carbonator – Large
This Carbonator is ideal for small scale soda/soft drink companies. It is of simple construction, hence maintenance and cleaning are very easy. Due to its special internal construction, quality of soda is high & better gas volumes can be achieved.
Co2 gas is fed into the carbonator through a Pressure Regulating Valve from the bottom. A highly efficient three piston SS pump feeds the carbonator with water. The pump has high quality durable seals that ensures very low maintenance of the pump. Water is fed by the pump to the carbonator from the top. Inside, there is a shower & a series of SS Plates mounted one on top of the other. The water is showered inside the carbonator and trickles down the plates. This ensures thorough saturation. The whole assembly is mounted on a SS stand. The carbonator is preinsulated to preserve water temperature. An Automatic Liquid Level Controller is also fitted to switch the motor on or off according to the level of water inside the tank.
The Pump and motor are fitted below the tank and covered on three sides to protect them from getting wet.
The size of the carbonator is 12” diameter x 5.0 ft height and output capacity is about 750 LPH. It can be altered for premix carbonation also.
Rinser with 24 Cups – for Glass Bottles
This unit is meant for rinsing 24 glass bottles at a time. It can be fitted on top of a cement/plastic or SS Tank. It has 24 nozzles fitted on SS pipes and connected to a central pipe with ball valve which is connected to a water source like overhead tank or pump. All contact parts are SS 304.
24 Bottles are kept upside down in the rubber cups. When the ball valve is opened, water jets into the bottles and rinses them. The rinse water falls back into the tank below and can be drained or recycled as required. About 48 bottles can be washed in a minute depending on the speed of the operators.
The unit requires very little maintenance. Generally the rinser is meant for 200 ml/ 250 ml /300 ml soda / soft drink bottles. But it can be altered to clean bottles of other shapes and sizes.
Brushing Unit with FRP / SS Cover – for Glass Bottles
The Brushing unit is used for cleaning glass bottles.
It is assembled on a stainless steel base plate with a Fiber Reinforced Plastic (FRP) SS cover. This cover protects a 1/2 HP I Phase 230 V 50 Hz motor. The motor is connected to two stainless steel shafts with pullies and V-belt.
This unit must be mounted on the center of a cement / stainless steel/plastic tank of height 2.5 –3 feet. The size of the tank depends on the space availability and the number of bottles to be washed. The brushing unit thus mounted has two brushes extending on one side and two brushes on the other. Therefore two people standing on opposite sides of the tank can at once clean 4 bottles.
Once the bottles are brought back from the market, they are soaked in another tank containing water with soap solution. This ensures that all dirt particles are loosened. The bottles are now ready to be brushed.
There are two types of brushes mounted on the unit. One long brush cleans the inside of the bottles and at the same time another brush cleans the mouth of the bottle where there is generally rust formation due to crown corks. Two persons can wash approximately 8-12 bottles per minute. This depends on the dexterity of the workers and dirtiness of the bottles.
After the brushing the bottles can be rinsed with plain water with the help of Rinser.
The Maintenance of the machine consists of greasing, V belt tightening whenever required and general cleaning.
Semi Automatic Washing Machine with Brushing Unit & Rinser – for Glass Bottles
This is a compact washing machine for glass bottles.
It consists of a Brushing unit mounted on one side of the machine. The unit has four brushes. An extra set of mouth cleaning brushes are also provided.
Two persons can stand and wash two bottles each on either side of the Machine.
After Brushing bottles are kept upside down on the adjoining rinser trays. These trays can hold 24 bottles each.
Once the tray is full, it is manually pushed and it goes to the next position where the bottles are rinsed with high speed jets of water. For this a 1/2 HP I ph pump is provided. Two rinsers with two tanks and two pumps are provided.
The machine can hold 7 trays in a row. The bottles are rinsed twice as they are pushed along the line.
The rinsed water falls back into the tanks at the bottom and is recycled. The tanks can hold about 100 liters of water. They are provided with water inlet & outlet ball valves.
Rinser with 12 / 24 Cups with Pump & Tray – for Glass Bottles
The Motorized Rinser is ideal for high-speed jet rinsing of PET / Glass bottles.
The pump must be used in case overhead tank is not available.
The Rinser is mounted on a portable SS table with a water collection tray.
Water connection is made to the inlet of the pump.
The outlet of the pump is connected to the three way ball valve of the Rinser.
The bottles are kept upside down in the rubber cups.
Ball valve is opened and the bottles are rinsed.
The rinsing water falls back into the collection tray and can be reused after filtration or drained.
Once the rinsing is over, the three way ball valve can be closed to load the
next lot.Mean while the pump is on and the pumped water is recycled back through the third port of the ball valve.
About 24 / 48 bottles can be washed per minute depending on the speed of the operator.
Soda / Soft Drink Machine – for Glass Bottles Manually Operated
The Machine is a one man Factory for making Soda and Soft drinks. Approximately 4000 bottles can be made in shift of 8 hours. It consists of the following main components:
Pump : It is a three piston pump with a capacity to pump approx. 450 liters per minute. A motor of ½ Hp is provided for the pump. The pumped water is fed into the Carbonator through a series of non-return valves. The fixed pumping speed ensures that the proper quantity of water is fed to the Carbonator and in turn the carbonating ratio between water and Co2 is maintained.
Pressure Regulating Valve : The PRV ensures that a fixed pressure of Co2 is fed into the Carbonator. In effect it is the heart of the machine and its maintenance and normal functioning is vital to the machine and quality of drink. The PRV can be adjusted for various pressures according to the soda/soft drink being made.
Carbonator : The Carbonator tank is made of stainless steel and houses a shower and series of SS plates. Gas and water are mixed in the tank. The shower and special SS plates inside ensure that the water passing through it is saturated thoroughly thereby ensuring optimum carbonation.
Filling head : First a crown cork is fixed inside the head. Then a bottle is kept on the bottle table. On lifting of a lever, soda flows into the bottle through a filling valve. To eliminate the air inside the bottle, a snifting valve is provided. Thus when the bottle is being filled, the air is eliminated through the snift valve. Due to this, some amount of soda also flows out through the snift valve. This is unavoidable. When the bottle is full, the lever is released and the foot pedal pressed for capping the bottle. The bottle is then removed and the next crown cork and bottle are kept and the whole process is repeated.
Stand : This is the main pillar of the machine. The Carbonator, pump, filling head and motor are all fitted onto it. The stand is made of Cast Iron thus ensuring a long life.
Motor : The motor is 1/2 HP either single phase or thee phase. This is a 1440- RPM motor. This RPM ensures that a fixed quantity of water is pumped into the Carbonator ensuring optimum carbonation.
To make Soft drinks : The syrup concentrate is previously filled into the bottle. The bottle is then kept on the machine and soda filled. The force with which the soda flows into the bottle (since soda is flowing from a higher pressure inside the carbonator to the atmospheric pressure of the bottle) ensures that the previously filled syrup mixes with the soda and the soft drink is ready. This method of making soft drink is called Post mix system.
Accessories supplied with the machine: A detailed catalog of the machine: An exploded view of each section of the machine helps in the maintenance and spares parts ordering. A separate section is devoted to the fault finding procedure for each section of the machine wherein are explained the various reasons of a complaint and the methods to tackle such problems.
A complete spanner set along with special spanners, tools and oil can are provided.
An extra set of washers is provided with the machine.
Soda / Soft Drink Machine – for Glass Bottles -Pneumatically Operated
The Machine is a one man Factory for making Soda and Soft drinks. Since this machine is pneumatically operated, it is easy to use and convenient. It requires an air compressor of 1.5 Hp. Approximately 4000 bottles can be made a in shift of 8 hours. It consists of the following main components
Pump : It is a three piston pump with a capacity to pump approx. 450 liters per minute. A motor of ½ Hp is provided for the pump. The pumped water is fed into the Carbonator through a series of non-return valves. The fixed pumping speed ensures that the proper quantity of water is fed to the Carbonator and in turn the carbonating ratio between water and Co2 is maintained.
Pressure Regulating Valve : The PRV ensures that a fixed pressure of Co2 is fed into the Carbonator. In effect it is the heart of the machine and its maintenance and normal functioning is vital to the machine and quality of drink. The PRV can be adjusted for various pressures according to the soda/soft drink being made.
Carbonator : The Carbonator tank is made of stainless steel and houses a shower and series of SS plates. Gas and water are mixed in the tank. The shower and special SS plates inside ensure that the water passing through it is saturated thoroughly thereby ensuring optimum carbonation.
Filling head : A Pneumatic cylinder is fitted for the filling and crowning operation. First a crown cork is fixed inside the head. Then a bottle is kept on the bottle table. The Filling lever is pressed & soda flows into the bottle through a filling valve. To eliminate the air inside the bottle, a snifting valve is provided. Thus when the bottle is being filled, the air is eliminated through the snift valve. Due to this, some amount of soda also flows out through the snift valve. This is unavoidable. When the bottle is full, the filling lever is released and the crown corking lever is pressed which operates another pneumatic cylinder. The bottle is then removed and the next crown cork and bottle are kept and the whole process is repeated.
Stand : This is the main pillar of the machine. The Carbonator, pump, filling head and motor are all fitted onto it. The stand is made of Cast Iron thus ensuring a long life.
Motor : The motor is 1/2 HP either single phase or thee phase. This is a 1440- RPM motor. This RPM ensures that a fixed quantity of water is pumped into the Carbonator ensuring optimum carbonation.
To make Soft drinks : The syrup concentrate is previously filled into the bottle. The bottle is then kept on the machine and soda filled. The force with which the soda flows into the bottle (since soda is flowing from a higher pressure inside the carbonator to the atmospheric pressure of the bottle) ensures that the previously filled syrup mixes with the soda and the soft drink is ready. This method of making soft drink is called Post mix system.
Accessories supplied with the machine : A detailed catalog of the machine: An exploded view of each section of the machine helps in the maintenance and spares parts ordering. A separate section is devoted to the fault finding procedure for each section of the machine wherein are explained the various reasons of a complaint and the methods to tackle such problems.
A complete spanner set along with special spanners, tools and oil can are provided.
An extra set of washers is provided with the machine.
Soda / Soft Drink Additional Filler – for Glass Bottles – Manually Operated
This is an additional filler required for filling Soda/soft Drinks in glass bottles.
It must be connected to an existing Carbonator with the help of a connecting hose provided with the machine.
This unit consists of a M.S. Stand on which are mounted the Filling Head and the Capping arrangement with the foot.
First a crown cork is fixed inside the head. Then a bottle is kept on the bottle table. On lifting of a lever, soda flows into the bottle through a filling valve. To eliminate the air inside the bottle, a shifting valve is provided. Thus when the bottle is being filled, the air is eliminated through the shift valve. Due to this, some amount of soda also flows out through the shift valve. This is navoidable. When the bottle is full, the lever is released and the foot pedal pressed for capping the bottle. The bottle is then removed and the next crown cork and bottle are kept and the whole process is repeated.
By using this machine in conjunction with the main filler, the production is doubled.
The Filling Head and the foot assembly are the same as in the main machine and therefore maintenance and operating procedures are also the same.
This machine can be supplied pneumatically operated also.
Soda / Soft Drink Additional Filler – for Glass Bottles – with Gear Box
This machine is used for soda/soft drink filling and crown capping of glass bottles. It can be used for filling 200 ml, 250 ml & 300 ml size glass bottles.It is only a filler / Capper and so needs to be connected to a Carbonator. Soda flows from the Carbonator to the machine. A pipe is provided for connecting the Carbonator and the machine.
The machine is semi automatic and so once a crown cork and bottle have been placed manually, the filling & crown capping take place automatically. The fill quantity can be slightly adjusted with the help of the inlet line ball valve and the snift valve. It is easy to use and the operator has to be able to coordinate the crown and bottle placing with the speed of the machine to ensure a smooth production.
The machine works on a 1 Hp I ph motor and suitable gear box. The output is about 400 bottles / hour. The speed of the machine is fixed and cannot be reduced or increased. It is built on a rigid Cast Iron stand and all its parts are made for rugged use. The maintenance is limited to regular oiling, change in gear box oil once in three months and change of washers, V Belt and springs as and when they wear out. Other than the above, it requires very less maintenance.
The main advantage of this machine is it is minimally laborious and so ideal for ladies, unskilled workers etc.
Soda / Soft Drink Filler – for Glass Bottles -PLC Controlled
This machine is used for soda/soft drink filling and crown capping of glass bottles. It can be used for filling 200 ml, 250 ml & 300 ml size glass bottles. It is only a filler / capper and so needs to be connected to a Carbonator. Soda flows from the Carbonator to the machine. A pipe is provided for connecting the Carbonator and the machine. The machine is semi automatic and so once a crown cork and bottle have been placed manually, the filling & crown capping take place automatically when a switch is pressed. The fill quantity can be slightly adjusted with the help of the inlet line ball valve and the snift valve. It is easy to use – the worker places a crown cap and a bottle on the bottle table
and presses a switch. The machine fills and crowns the bottle automatically. The filled bottle is removed and the cycle is repeated. The filling and crowning times can be adjusted with the help of the PLC (Computer Controlled).
The machine is pneumatically operated and so requires a 1.5 Hp Air compressor. The output is about 400 bottles / minute. It is built on a rigid stand and all its parts are made for rugged use.
The maintenance is limited to regular oiling, change of washers, V Belt and springs as and when they wear out. Other than the above, it requires very less maintenance. The main advantage of this machine is it is minimally laborious and so ideal for ladies, un skilled workers etc.
5 HEAD GLASS BOTTLE HEAVY DUTY ROTARY ATOMIZED CSD FILLING MACHINE EKTA BRAND
The machine equipped with Counter Pressure (CSD) Filling Technology delivers the quality as per the industrial standards as compared to the top brands in the market. Counter Pressure filling is important as it helps in the process of evacuation of unwanted gases, pressuring the bottle with CO2 gas and filling the carbonated soda in the glass bottle. Due to large diameter Monoblock rotary system, the settling and shifting process is very efficient and larger quantity of soda/soft drink can be filled very efficiently. It normally fills standard Carbonated Glass Bottles with sizes such as 200ml , 250ml & 300ml Glass Bottles. It can also fill any unique designed bottles as per the standard bottle shape norms.
The average speed of 5 Head Rotary systems is around 20 BPM (Bottles per minute). It can produce up till 50 crates (cases of 24 bottles) in an hour.
High Grade SS Material is used with Food grade SS 304 contact parts with very heavy filling valves and also Fitted With Best Quality Electric & Electronic Components, the maintenance in the machine is very low.
Hand Operated Batch Coding Machine – Manual
The Hand Operated Batch Coder is a handy machine for printing batch umber, MRP, date of mfg etc as required. It can print three or four lines. The unit is available for printing on various surfaces like plastic, metal, wood, paper, ceramic and glass – onbottles, lids, caps, jars, labels, laminated cartons, tins, cups etc. It can print on flat and curved surfaces. For each application a model is available.
A complete set of alphabets, numbers and symbols are provided. These are available in sizes from 2 mm to 10 mm depending on whether they are metallic or rubber. A bottle of special fast drying ink is supplied with the coder.
The machine is also supplied with a wooden base for printing on soda/soft drink glass bottles. It is also available pneumatically operated. The machine can be fitted on automatic Form Fill Seal Packing machines for printing on pouches as they are formed, filled and packed.
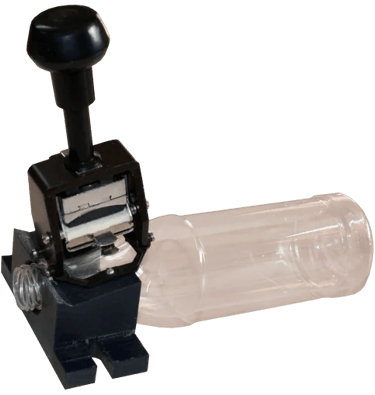
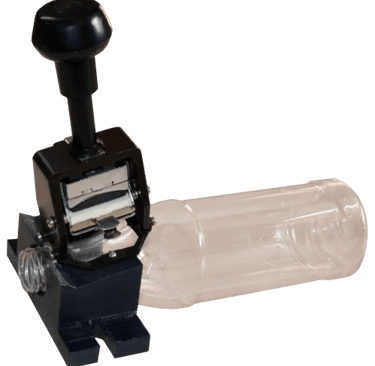
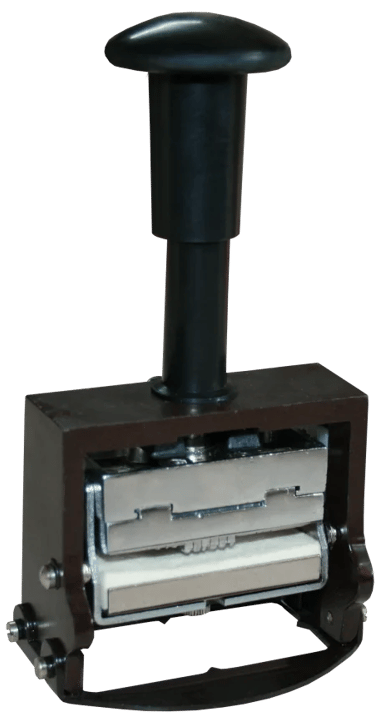
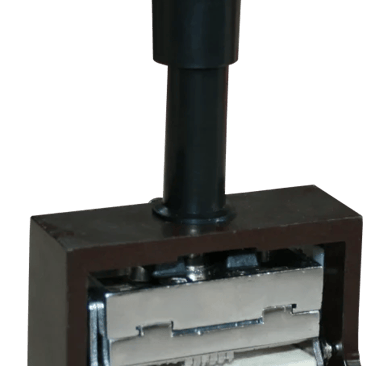
Gas Volume Tester – for Glass & PET Bottles
This is an easy to use unit for determining the ‘Gas Volumes’ of a soda /soft drink.
‘Gas volume’ is a unit determined by the pressure inside a bottle and the temperature of the liquid.
The Gas Volume Tester is basically a quality-checking unit.
One or two bottles are taken out from the production line at regular intervals.
The Tester is first clamped on the bottle to be checked.
Then the bottle is punctured with the spindle by rotating the knob and the pressure noted on the pressure gauge.
The Tester is then removed, bottle opened and the temperature of liquid checked.
Both values are noted and the ‘gas volumes’ found by referring chart provided.
Soda and various soft drinks have varying ‘gas volumes’ and the values have to be adhered to get the best quality.
The Tester is available for both glass & PET bottles.
It is made of SS 304
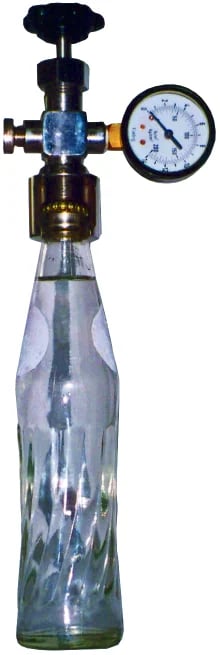
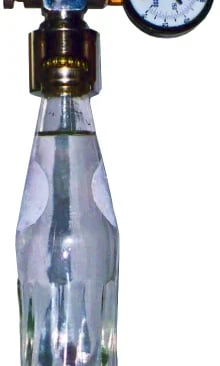
Single Head Goli Bottle Filler – Manual
MGI Goli Bottle Filler is a simple easy to use machine. This is a single head filler.
It is connected to a Carbonator with the help of a hose provided. One Goli bottle is kept between the filling head and bottle table by pressing the long lever. It is held there by a spring. The filling head is turned up side down and the filling lever is pressed, Once the bottle is filled, the bottle is taken off by pressing the long lever again.
The machine requires very little maintenance restricted to change of head washer and O rings inside the filling head. This can done by user.
About 6-8 bottles can be filled per minute depending on the speed of the operator. A shift valve is provided to release excess pressure to reduce bottle breakage. A half round cover is provided to avoid injury to operator due bottle breakage during filling.
The stand of the machine is of MS (powder coated) and all the contact parts of the machine are SS 304.
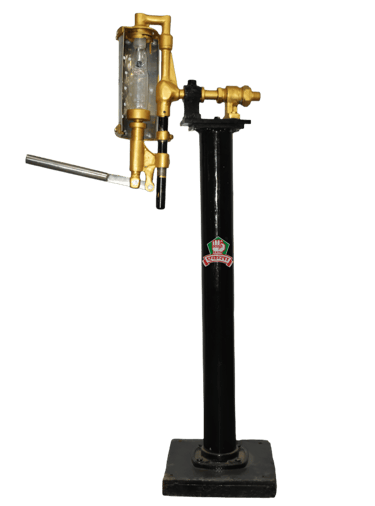
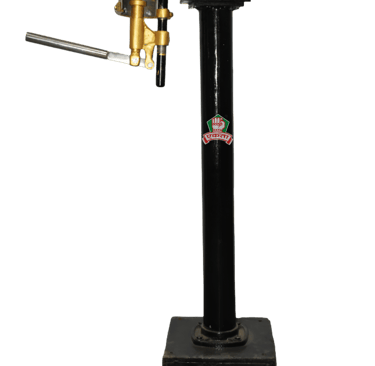
Three Bottle Goli Soda
(CODD) Bottle Machine Manual / Motorised
The Three Bottle Goli Soda Machine can Carbonate three bottles at a time. It is a very robust table top manually operated machine. The machine is made out of Cast Iron to last many years. The machine is supplied with a pressure guage, CO2 Regulator, CO2 control valve and a copper pipe to connect it with a CO2 gas cylinder. The unique design and method of use ensures a very strong soda.
The front door of the machine is opened and three filled bottles are placed on the three bottle tables provided. The bottle tables are locked from beneath. The door is closed. The CO2 valve is opened and the handle on the right side is turned several times. As the chamber rotates, CO2 mixes with the drink. The more it is rotated, the more the CO2 mixes with the liquid and stronger the soda. The door is then re-opened and the bottles are taken off.
The machine can also be supplied with a 1/2 HP I ph motor and suitable gear box to rotate it automatically. A control panel with a timer is provided for setting the rotation time.
About 3-6 bottles can be carbonated per minute depending on the speed of the operator. Soda and soft drinks can both be made.

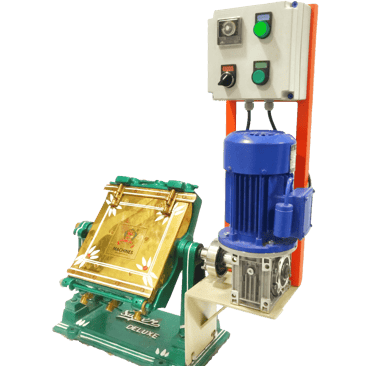
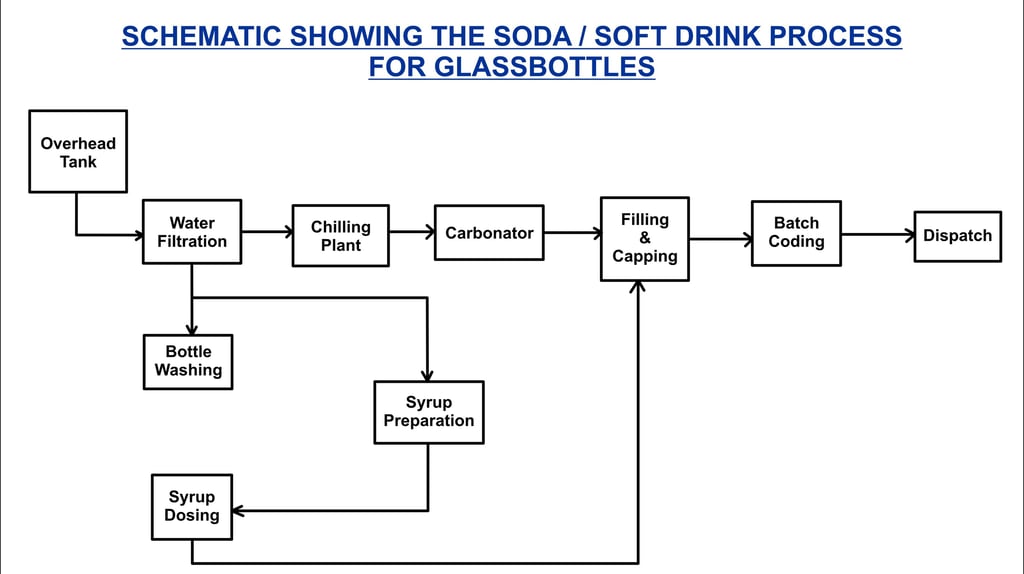
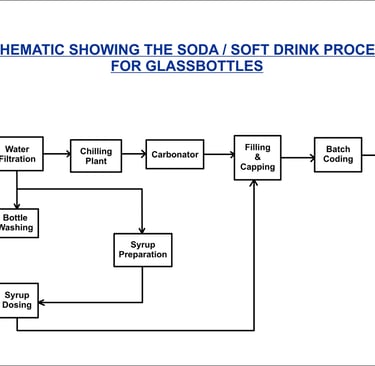
Semi Automatic Rotary Glass / PET Goli
(CODD) Bottle Soda / Soft Drink Filling Machine
This is a unique one of its kind semi automatic rotary filler machine for CODD bottles. The speciality of the machine is its rotary motion which fills the bottle and automatically locks the ball immediately after filling is over.
It is a sturdily built machine and fabricated fully of SS 304. The machine has a rotating plate on which nine filling heads are fitted. Two people are required – one for keeping the bottle on the bottle table when the head is in upright position and one for removing the filled bottle after one revolution. The bottle clamping and filling are pneumatically done and so an air compressor of 3 HP is required. A control panel is provided with a RPM control so that the rotation can be slowed down or speeded up as required. An emergency switch is provided for immediate stopping of the rotary plate.
Each filling head is housed in a stainless steel cover. The front & side covers of the machine are also designed so that it is easy to keep and take off the bottles from the rotating plate.
Both these provisions also ensure that the operators are not injured if a bottle breaks. In case a bottle does break during filling, the machine can be stopped for a few seconds and the head can be cleaned. The machine can be resumed quickly. Each filling head is provided with a seperate air valve which can be shut off in case the head requires some maintenance. In the meanwhile the machine can continue to be used. A connection is provided behind the machine to connect it to the carbonator. An FRL is also provided for setting the correct air pressure. The machine has a 1 HP III ph motor and suitable gear box.
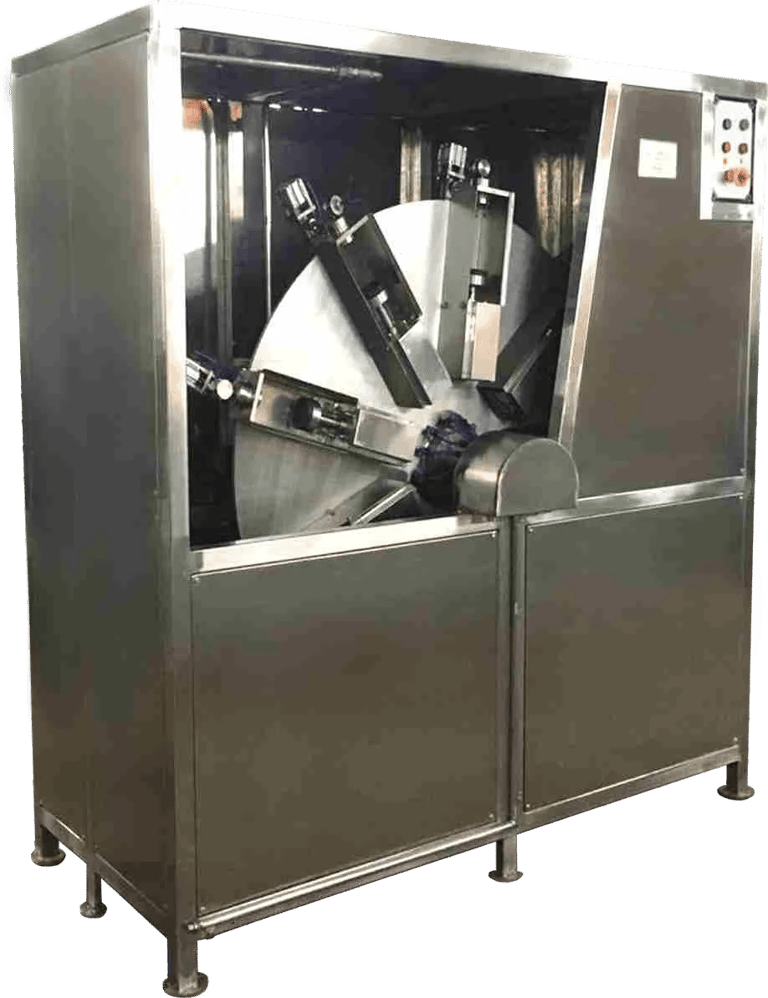
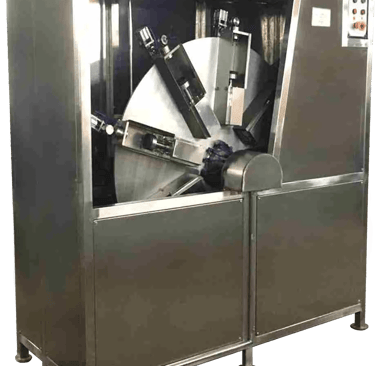