Ultra Violet Water Filter
Ultra Violet Water Filter System is ideal for filtration of Bore well and Well water. It is a 3-in-1 filter system.
It has a 10 micron filter cartridge which removes all visible dust particles. The water then flows through an activated Carbon Cartridge which removes chemicals and odour. Then the water flows through the UV chamber where two UV lamps are provided. They help to eliminate bacteria , germs, pathogens etc.
The filter can process about 500 litres of water per hour. It can be connected to an overhead tank and the water will flow through it by gravity. There is no need for pumps.
It is wall mountable and easy to assemble. It requires very little maintenance and is user serviceable.
It is an ideal unit for Soda / Soft drink makers, juice processing factories, hostels, hotels, etc. and wherever bulk drinking water is required.
Soda/Soft Drink Machines for Pet Bottles
Sand Water Filter
The Sand Water Filter is used for filtering out all visible dust particles from water. To a certain extent, It also removes chemicals and odour from water.
The filter is made of Fibre Reinforced Plastic (FRP) and is therefore maintenance free. The FRP material is ideally suited for water filtration tanks and is very strong and rigid. The tank requires no painting and does not rust.
Water passes through three layers of special Quartz stones and sand and a layer of Activated Carbon. A 10 micron filter cartridge is also provided at its outlet to remove tiny dust particles.
A system of pipes and ball valves is provided which are attached to the main portion of the tank. The filter can be connected to an overhead tank and the water flows through the filter by gravity. About 500 litters of water can be filtered per hour.
Other than periodic backwash and a change of carbon, the filter requires very little maintenance.
It is an ideal unit for Soda /soft drink makers, juice processing factories, Hostels, Hotels etc and wherever bulk drinking water is required.
Reverse Osmosis Filter Unit
Reverse Osmosis is a technology that is used to remove a large majority of contaminants from water by pushing the water under pressure through a semipermeable membrane. The unit consists of a comprehensive set of filters like –
Prefilter to remove dust
Carbon filter to remove chemicals and other off smells
Ultra violet lamps to kill harmful bacteria and viruses
Reverse Osmosis filter unit to remove contaminants
Ozonator (Optional)
Other filters can be added depending on the inlet water quality.
The whole unit is mounted on a skid so it is easy to transport and can be quickly installed. Each filter unit is connected to the next in line with necessary pipes and fittings. Pumps are also provided.
The different filter stages are selected depending on the quantity of water available and so a Water Test Report is essential. Based on the report, the system can be tailored to get best results.
The unit is easy to install and requires minimum maintenance. It is made for reliable performance.
3 Ton Air-Cooled Chiller Unit designed for small to medium-scale industrial or commercial cooling applications. The unit features a high-speed axial fan mounted in a blue powder-coated steel body, ensuring efficient air flow and heat dissipation. On the right side is an integrated electronic control panel, labeled with essential safety and operational indicators. The panel includes power indicators, emergency stop, automatic temperature control, and a digital display for temperature monitoring and settings. This chiller operates on a 3-phase, 415V power supply, suitable for industrial-grade power input. The unit is compact and robust, ideal for continuous operation in environments like plastic molding units, chemical processing, cold rooms, or laser cutting machines. It utilizes eco-friendly refrigerants and is designed with built-in overload protection, phase failure safety, and temperature regulation, ensuring smooth and safe operation. Its compact design makes it easy to install and maintain, while the external wiring and reinforced legs provide additional support and durability in demanding industrial settings.
5-ton Emerson Copeland air-cooled condensing unit, specifically designed for commercial and industrial cooling applications. This compact and efficient system features dual axial fans that ensure effective heat dissipation, along with a high-performance Copeland compressor, known for its durability and energy efficiency. The unit operates on a 3-phase 380–415V, 50 Hz power supply and uses eco-friendly refrigerants such as R-22, R-407C, or R-410A, depending on the configuration. It is mounted on a sturdy metal frame, which also houses a centrifugal water pump connected through insulated piping—indicating that this unit is likely used in a water chiller system or cold room application. The system is capable of handling a 5 TR (tons of refrigeration) load, making it ideal for medium-scale cooling requirements. It includes a digital control panel for temperature and pressure monitoring, along with standard safety features like overload protection and phase failure detection. This 5-ton unit delivers reliable performance with easy maintenance, making it a practical choice for commercial HVAC, cold storage, or process cooling setups.
Medium Size Carbonator – Regular Quality
This Medium Size Carbonator is a reliable and efficient solution designed for carbonating beverages like soda, water, and other soft drinks. Crafted with precision, it delivers consistent carbonation results, ensuring excellent taste and fizz retention in every batch. The unit is built using regular quality yet durable materials, offering a balance between affordability and functionality for medium-scale beverage production operations.Mounted securely on a robust MS (Mild Steel) stand, the carbonator is equipped with an automatic control system that streamlines the carbonation process by managing pressure, CO₂ flow, and liquid levels efficiently. This automated operation enhances productivity, reduces manual effort, and ensures safety during use. Ideal for businesses seeking a dependable carbonation unit without compromising on performance or quality.
Big Size Carbonator – Regular Quality
This Big Size Carbonator is a robust and efficient carbonation system designed to meet the needs of high-volume beverage production. Crafted with a large-capacity stainless steel tank, it is ideal for carbonating water, soda, and other soft drinks on an industrial scale. Despite its regular quality build, it ensures stable performance, consistent carbonation, and long-term reliability.The carbonator is mounted on a strong Mild Steel (MS) stand for added durability and support. It features an automatic control system that regulates pressure, CO₂ flow, and fluid dynamics with precision, making the process seamless and user-friendly. Perfect for businesses looking for an affordable yet high-capacity carbonation solution, this unit delivers both performance and productivity without compromise.
Automatic Carbonator – EKTA Royal Model
The EKTA Royal Model Automatic Carbonator is a premium, high-performance carbonation system designed for seamless integration into modern beverage production lines. Engineered for precision and efficiency, this unit ensures optimal carbonation levels and consistent output to meet industrial demands. It is mounted on a sturdy Stainless Steel (SS) stand, offering both strength and corrosion resistance for long-term operation in demanding environments.Equipped with a sophisticated SS control panel, the machine features both automatic and manual operation modes, allowing for flexible control based on production needs. Its intelligent design ensures the continuous and sufficient supply of carbonated liquid to the filler, minimizing downtime and enhancing productivity. Ideal for professional bottling plants, the EKTA Royal Model combines reliability, durability, and advanced automation for a superior carbonation experience.
Rinser with 12 Cups – for PET Bottles
This unit is meant for rinsing 12 PET bottles at a time. It can be fitted on top of a cement/plastic or SS Tank. It has 12 nozzles fitted on SS pipes and connected to a central pipe with ball valve which is connected to a water source like overhead tank or pump. All contact parts are SS 304.
12 Bottles are kept upside down in the nylon cups. When the ball valve is opened, water jets into the bottles and rinses them. The rinse water falls back into the tank below and can be drained or recycled as required. About 24 bottles can be washed in a minute depending on the speed of the operators. The unit requires very little maintenance.
The Rinser can wash any size of PET bottle from 200 ml to 2000 ml. It can also be altered to suit bottles of different mouth diameters, shapes and sizes
Rinser with 2 Nozzles – Press Type for PET Bottles
This rinser is ideal for quick high pressure jet rinsing of PET bottles with pressurized water. A ½ Hp I ph monoblock pump is fitted on the machine for this. It can be used for rinsing all Pet bottles from 200 ml to 2000 ml. It consists of a stand and tray on which the two nozzle rinser is fitted. The pump is installed below the tray. An NRV is fixed on the pipe line from pump to rinsers so that when the bottles are not rinsed, the water flows back to reservoir. So the pump can run continuously and need not be switched on and off.
The Rinser consists of two spring loaded nozzles. When two bottles are pressed upside down on the nozzles, the bottles are flushed with a jet of water. The rinse water falls back in to the tray below from where it can be drained or recycled as required.
The water collection tray, stand and rinser nozzles are all made of SS 304. About 12-14 bottles can be rinsed per minute – but this depends on the speed of the operators.
Rinser with 12 / 24 Cups with Pump & Tray for PET Bottles
The Motorized Rinser is ideal for high-speed jet rinsing of P ET bottles.
The pump must be used in case overhead tank is not available.
The Rinser is mounted on a portable SS table with a water collection tray.
A monoblock pump is provided to jet the water into the bottles.
Water connection is made to the inlet of the pump.
The outlet of the pump is connected to the three way ball valve of the Rinser.
The bottles are kept upside down in the rubber cups.
Ball valve is opened and the bottles are rinsed.
The rinsing water falls back into the collection tray and can be reused after filtration or drained.
Once the rinsing is over, the three way ball valve can be closed to load the next lot.
Mean while the pump is on and the pumped water is recycled back through the third port of the ball valve.
About 24 / 48 bottles can be washed per minute depending on the speed of the operator.
Motorised Liquid Stirrer
The Stirrer is basically a mixer with a fan blade at the bottom.
It is used for stirring /mixing liquids like juices, syrups, curd etc.
It is also most useful in the food, rubber, chemical and other industries where a homogeneous mix of the liquid is critical to product quality.
The Stirrer consists of a high-speed motor mounted on a bell housing from where four stainless steel rods extend down and support a frame of stainless steel plates with holes.
The motor shaft is connected to the fan blade at the bottom with a central stainless steel shaft.
The stirrer is hung inside the container holding the liquid with the help of a wire rope and winch provided. The bottom of the stirrer is kept about six inches above the bottom of the container.
When the motor is switched on, the central shaft turns and rotates the blade.
The blade pushes the liquid through the holes in the stainless steel frame and thus the liquid is broken up into bits and mixes well.
The stirrer is used for 10 – 30 minutes as required.
The size of the stirrer may vary according to the quantity of liquid to be mixed at a time.
The stirrer has an advantage over the conventional mixers in that the liquid is mixed by breaking it up rather than making it revolve in the container.
This Stirrer with a ½ Hp I Ph motor can mix about 100 liters of liquid at a time.
If the liquid is too viscous or foaming type, the Stirrer can be specially made to suit the liquid quantity & application required.
Soda / Soft Drink Filler for – PET Bottles Manually Operated Single Head (Direct Filler)
This table-mounted unit is an additional filler used for filling soda /soft drinks in PET bottles.
This machine must be connected to a Carbonator.
PET bottles of size 200 ml to 2000 ml can be filled.
No mounting adjustments are required.
The bottle is placed on the bottle holding plate and the bottom lever pressed.
When the filling valve lever is pressed, soda starts flowing into the bottle.
When the bottle is full, the filling lever is released. The bottom lever is also released and the bottle can be taken off.
T o make soft drinks, the bottles are pre-filled with required amount of syrup concentrate. Then soda is filled on the machine – the soda and syrup mix inside the bottle to make soft drink.
A ‘Snift’ Valve is fitted to release the air inside the bottles during filling.
The machine requires very little maintenance except for washers and springs that generally wear out.
5-Head Heavy Duty PET Bottle EKTA Rotary Atomized Filling Machine
The EKTA Rotary Atomized Filling Machine is a high-performance, 5-head heavy-duty solution specifically designed for Carbonated Soft Drink (CSD) filling applications. Built for durability and efficiency, this machine is capable of filling PET bottles ranging from 200 ml to 2 litres with utmost precision. It is fitted with top-quality electric and electronic components, ensuring reliable and consistent performance under rigorous operating conditions.The machine features high-grade valves that guarantee accurate and hygienic filling, making it ideal for carbonated beverages like soda. Designed with industrial-scale production in mind, it delivers an impressive average speed of 20 bottles per minute (BPM) for 200 ml soda bottles, ensuring a smooth and fast bottling process.This rotary atomized system not only enhances the filling efficiency but also minimizes wastage and downtime. It is an excellent choice for beverage manufacturers looking for a robust, long-lasting, and efficient filling solution that meets modern production standards.
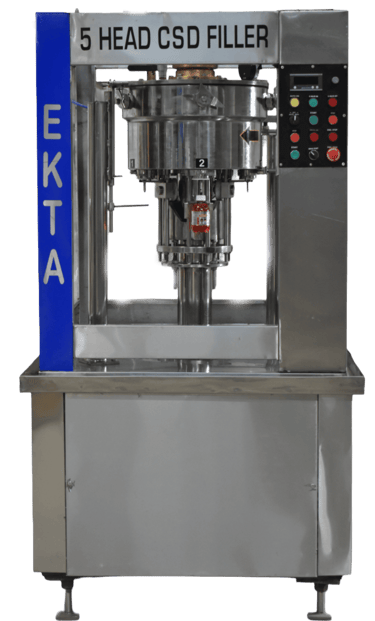
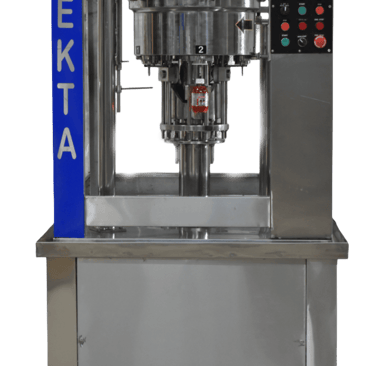
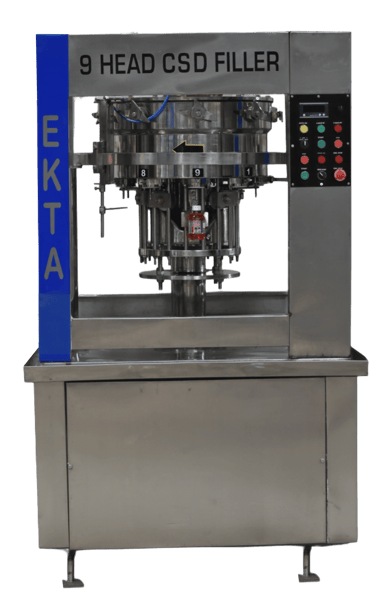
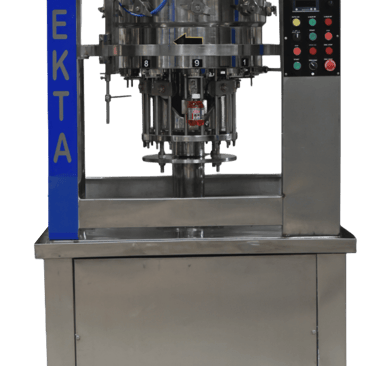
9 HEAD HEAVY DUTY PET BOTTLE EKTA ROTARY ATOMIZED FILLING MACHINE
The 9 Head Heavy Duty PET Bottle EKTA Rotary Atomized Filling Machine is a high-performance solution designed for efficiently filling carbonated soft drinks (CSD) in PET bottles ranging from 200ml to 2 liters. Built with premium quality stainless steel, this machine ensures durability, hygiene, and smooth operation even in high-demand environments. It features nine precision filling heads and a rotary atomized system that delivers splash-free and accurate filling with minimal wastage. With an impressive average speed of 40 bottles per minute (BPM) for 200ml soda, it is ideal for medium to large-scale beverage production lines. The machine is equipped with top-grade electric and electronic components, along with high-quality valves, ensuring reliability, energy efficiency, and long-term performance. Its user-friendly control panel allows for easy operation and real-time monitoring, making it a trusted choice for efficient and consistent beverage bottling.
The 12-Head Heavy Duty PET Bottle Ekta Rotary Atomized Filling Machine
is a high-performance solution designed specifically for filling carbonated soft drinks (CSD) ranging from 200ml to 2 litres. Built with a strong and durable structure, this machine features a rotary atomized filling system that ensures splash-free and foam-free filling, preserving the carbonation and quality of the beverage. With 12 precision-engineered filling heads, it offers an impressive average speed of 40 bottles per minute for 200ml soda. The machine is equipped with top-quality electric and electronic components, including advanced PLC controls, sensors, and hygienic food-grade valves to deliver consistent, reliable performance in demanding production environments. Its stainless-steel construction and compatibility with various PET bottle sizes make it an ideal choice for beverage manufacturers seeking speed, accuracy, and long-term durability. Optional integration with capping, labeling, and printing units makes it a complete bottling line solution.
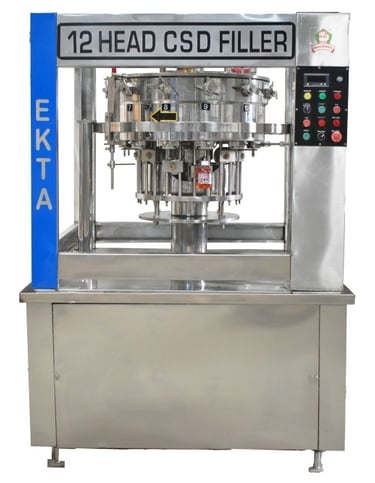
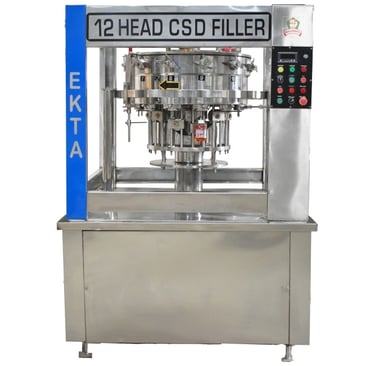
PET Bottle Capping Machine – Motorised
This Capping Machine is used for capping PET bottles.
Any PET bottle can be capped. However the capping die may vary according to the cap diameter.
The Capper is powered by a 1/2 hP I PH motor with an attached gearbox.
The capping die is fitted on the output shaft of the gearbox. The die rotates at an approximate speed of 100 RPM.
After the PET bottle is filled, the cap is placed on it and the bottle with cap is pressed into the rotating Die.
The rotating Die then automatically h olds the cap and tightens the cap on the bottle. This whole operation takes about 4-5 seconds depending upon the dexterity of the operator.
A torque setting is provided to ensure the correct tightness of the cap. The amount of tightness required can be adjusted with the help of spring-loaded ball provided.
The advantage of the machine is that all the bottles are evenly tightened and operator fatigue is low.
An optional stand is available to fix the machine on a wall or table.
About 10 bottles can be capped per minute.
PET Bottle Capping Machine – Pneumatic
This is an easy to use machine for capping plastic bottles – fast. It is very handy and portable and can cap about 10-12 bottles per minute depending on the user’s speed. It must be connected to an air compressor. An FRL must be fitted in the pipe from air compressor to the machine.
It has a torque setting which ensures that the cap is tightened exactly as much as required. The cap is placed on the bottle and the Pneumatic Capper is pressed on the cap. It is tightened and stops once the set torque is reached.
It’s unique features are:
Being pneumatically operated , it requires very little maintenance except for oil in the FRL.
Easy to use and requires very little skill.
It is light weight and portable.
Uses minimum quantity of air only when it is actually capping.
No electrical connection and therefore free from short circuits and carbon brush problems.
Crown Capping Machine – Hand Operated Table Model – for Glass Bottles
This is a handy table top machine for crown corking glass bottles. It can be installed on a table and is easy to use.
A glass bottle is placed on the bottle table. The height of the crowning Die is adjusted to suit the bottle height. A crown is placed below the Die. It is held on by a magnet. The handle on the front is pressed downwards and the bottle is crowned.
The machine is robust and can crown about 7-8 bottles per minute depending on operator speed.
Crown Capping Machine Pneumatically Operated Table Model – for Glass Bottles
The machine is a table top model crown capping machine pneumatically operated. It can be installed on a table top.
The machine is connected to an air compressor. A crown is placed on the Die where it is held by a magnet. A bottle is placed on the bottle table and the hand lever is operated. After capping the bottle can be taken off for the next bottle. About 6-8 bottles can be capped per minute depending on the speed of the operator. Since it is pneumatically operated the bottles are crowned evenly and accurately. The pressure of crown capping can be set as required depending on the thickness & quality of the crown.
The machine is compact and portable. Air consumption is minimal and maintenance is limited to change of crowning Die when it gets worn out and change of oil in the FRL which controls the air quality and pressure from the compressor. The machine can cap glass bottles of all sizes from 200 ml to 750 ml.
Hand Operated Batch Coding Machine – Manual
The Hand Operated Batch Coder is a handy machine for printing batch number, MRP, date of mfg etc as required. It can print three or four lines. The unit is available for printing on various surfaces like plastic, metal, wood, paper, ceramic and glass – on bottles, lids, caps, jars, labels, laminated cartons, tins, cups etc. It can print on flat and curved surfaces. For each application a model is available.
A complete set of alphabets, numbers and symbols are provided. These are available in sizes from 2mm to 10 mm depending on whether they are metallic or rubber. A bottle of special fast drying ink is supplied with the coder.
The machine is also supplied with a wooden base for printing on soda/soft drink glass bottles. It is also available pneumatically operated. The machine can be fitted on automatic Form Fill Seal Packing machines for printing on pouches as they are formed, filled and packed.
Automatic Inkjet Coding Machine with Conveyor
This is an “ANSAR” make INKJET Coding Machine model PRO S for printing on porous & non-porous surfaces like PET, metal, plastic, wood & paper. It can be used for printing on bottles, caps, labels, boxes, bags etc.
It has the following unique features:
Cartridge is suitable for 2.5 lakhs to 2.75 lakhs prints of three lines each which makes it extremely cost effective.
Display of the printer of 3.5 inch LCD screen with LED back light
User interface has a simple and easy to use operating system
Input device is a pocket sized IR remote key pad
Available languages are Chinese, English, German, Spanish etc,
Size of the of the printer is 119 mm x 78.8 mm x 76.0mm
Weight is 550 gms
Mounting orientation can be horizontal or vertical
Operating temperature is 5 degrees Celsius to 50 degrees Celsius
Data interface is RS485, USB port
Can be integrated with FFS machines, band sealers, taping machines and other packing machines for printing on labels, bags and pouches
The most significant advantage of the U2-ProS and TIJ printers in general is that they are virtually zero maintenance devices. Once a cartridge is exhausted, it merely has to be replaced with a new piece. There is no ink reservoir, make-up or complicated parts that need regular replacement like most large character or CIJ printers.
Shrink Wrap Tunnel with Plastic Film Wrapper for – Packing PET Bottles
This is a Shrink Film Wrapper and Heat Shrinking Machine for packing PET Bottles. Shrink Wrapping is now a days considered a cheaper and better option in place of cardboard boxes.
The machine is in two parts – the Shrink Film Wrapper and the Heat Shrink Tunnel. The Wrapper has been provided with a set of guides to be adjusted according to the number and size of bottles to be packed. The Shrink Tunnel is provided with a metallic mesh conveyor to withstand temperature, suitable heaters, temperature sensor and controller to maintain the required temperature and a set of fans to circulate the heat inside the tunnel. The machine is controlled by a central control panel where the temperature inside the tunnel, the speed of the conveyor, the fans and other functions can be easily controlled.
The PET bottles are kept on a table on the Wrapper. The operator then presses a switch and the machine automatically wraps the shrink film over them. The bottles are now moved forwards by the machine. Meanwhile the operator can keep the next set of bottles. The first set of wrapped bottles now move into the shrink tunnel. The shrink wrapped bottles come out of the other end of the tunnel where another fan cools down the plastic film. The packed bottles are now taken off. The process continues as each set of bottles are placed one after the other
The wrapping of the film takes place pneumatically and so an air compressor is required. It has height adjustable washers on each of its legs so the Wrapper and the Tunnel can be aligned on the same level. It has a set of holders on the top and at the bottom to hold the shrink film roll which have to be fixed.
The width of the film rolls will vary according to the number and size of bottles to be packed.
The machine has a sturdy powder coated MS body built for a long life. Both the Wrapper and Shrink Tunnel have wheels below so they can be moved easily. With minor adjustments that can be done quickly, PET bottles of any size from 200 ml to 2000 ml can be packed. Note that the machine can be used for other items like cardboard boxes, glass bottles, regular and irregular shaped objects etc can also be packed.r
Gas Volume Tester – for Glass & PET Bottles
This is an easy to use unit for determining the ‘Gas Volumes’ of a soda/soft drink.
‘Gas volume’ is a unit determined by the pressure inside a bottle and the temperature of the liquid.
The Gas Volume Tester is basically a quality-checking unit.
One or two bottles are taken out from the production line at regular intervals.
The Tester is first clamped on the bottle to be checked. Then the bottle is punctured with the spindle by rotating the knob and the pressure noted on the pressure gauge.
The Tester is then removed, bottle opened and the temperature of liquid checked.
Both values are noted and the ‘gas volumes’ found by referring chart provided.
Soda and various soft drinks have varying ‘gas volumes’ and the values have to be adhered to get the best quality.
The Tester is available for both glass & PET bottles.
It is made of SS 304.
Semi Automatic PET Bottle Capper Pneumatically Operated
This a timer based Pneumatic PET Bottle Capper. The capper is basically a “Chicago Pneumatic” torque tightening tool. It is fitted on a stand with a timer. The worker keeps a filled bottle with the cap, on a neck holding plate. The plate goes up and down at the time set by the operator. The machine tightens the cap at the torque set on the machine and bottle is brought down. The capped bottle can be taken off and the next bottle is kept. Since the capper is fitted on the machine it need not be manually held — thus reducing operator fatigue.
It’s unique features are:
Being pneumatically operated, it requires very little maintenance.
Easy to use and requires very little skill.
It is light weight and portable.
Uses minimum quantity of air only when it is actually capping.
No electrical connection and therefore free from short circuits and carbon brush problems.
The time between each capping can be set as per the convenience of the operator.
About 12-15 bottles can be capped depending on the speed of the operator.
A 1 HP air compressor is required for this machine.
Table Top Soda/Soft Drink Maker
The Table Top Soda/Soft Drink Maker is a unique compact machine ideal for way side shops, stalls, cottage level industries etc for making carbonated drink and serving on the spot. It is easy to use and does not require any training except for a few basic concepts. The machine is available for both glass and PET bottles.
A bottle is filled with water & premixed flavours. The bottle is then fitted on the machine. A lever is pressed for releasing the CO’ into the bottle. The liquid is carbonated and the bottle can be taken off. A fast workercan do about 3-4 bottles per minute.
The main features of the machine are:
CO’ is stored in the MS tank of the machine which is tested for high pressure.
The CO’ inlet valve on the machine is of good quality.
It is easy to use.
PET bottles of all sizes from 300 ml to 2000 ml can be used without any adjustment or setting.
The machine requires very low maintenance except for change of washers once in a few days depending on the daily volume of usage.